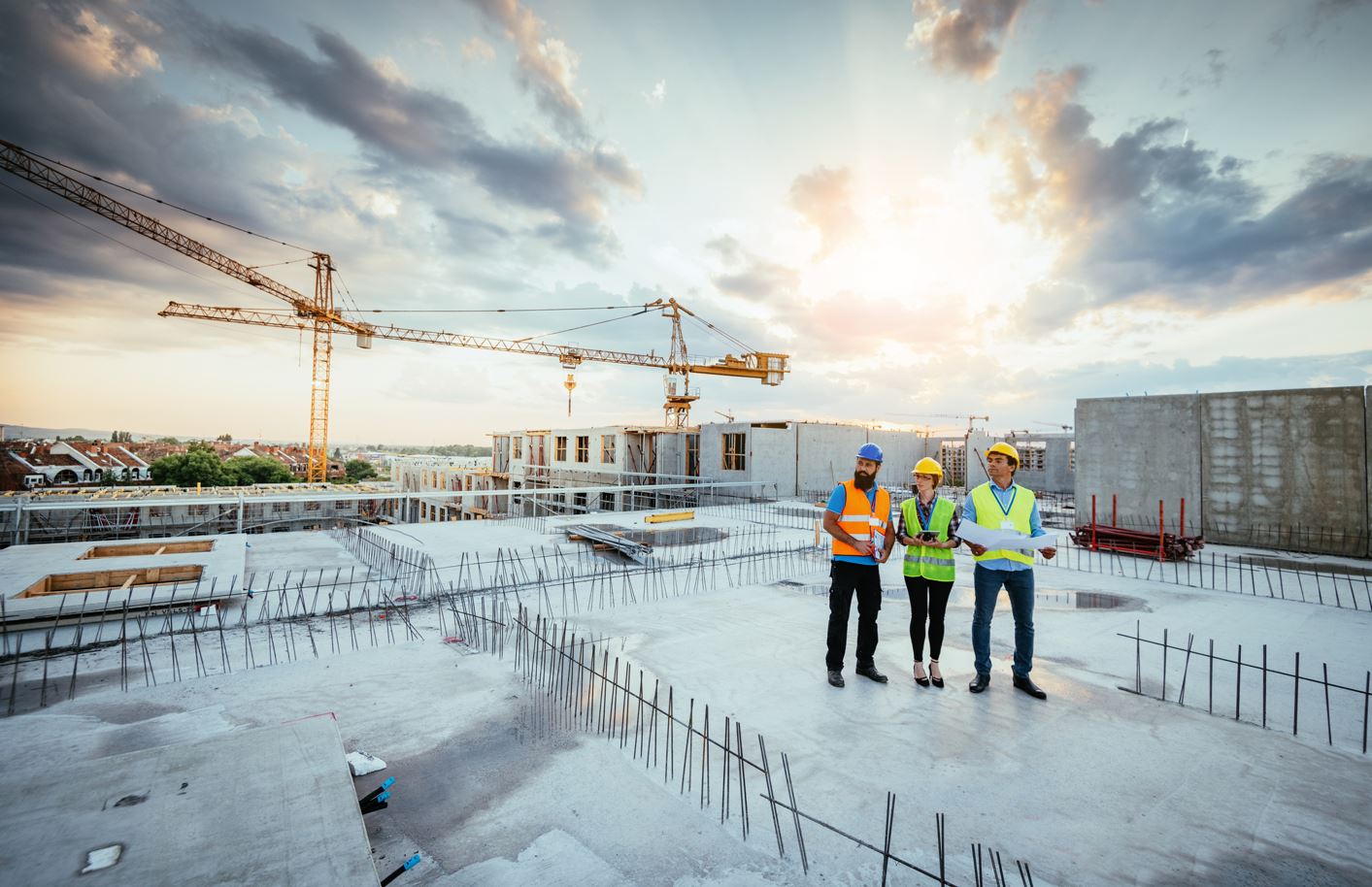
An international research group is building a case for more sustainable concrete by replacing synthetic reinforcement materials with natural fibres and materials from difference waste streams.
The latest Flinders University-led study, with experts from the US and Turkey, demonstrates how geopolymers reinforced with renewable natural fibres and made with industrial by-products and waste-based sands from lead smelting or glass-making can match the strength, durability and drying shrinkage qualities of those containing natural sand, which in turn consumes more raw resources and generates extra emissions in its processing.
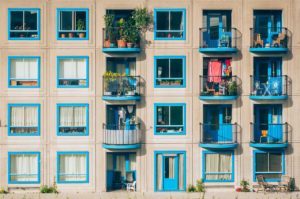
Conventional concrete is the most widely used construction material, with 25 billion tonnes used every year. It consumes about 30% of non-renewable natural resources, emitting about 8% of atmospheric greenhouse gases and comprising up to 50% of landfill.
Lead researcher, Flinders University civil and structural engineering researcher Dr Aliakbar Gholampour, says the promising findings have significant potential for the use of natural fibres in the development of structural-grade construction materials, in which binder and aggregate are replaced by industrial by-products and waste-based materials.
Test results showed that geopolymers using waste glass sand exhibit superior strength and lower water absorption than those containing natural river sand – while lead smelter slag (LSS)-based geopolymers have lower drying shrinkage compared to geopolymers prepared with natural river sand.
As well, natural fibres such as ramie, sisal, hemp, coir, jute and bamboo were incorporated in testing experiments.
The geopolymers containing 1% ramie, hemp and bamboo fibre – and 2% ramie fibre – exhibit higher compressive and tensile strength and a lower drying shrinkage than unreinforced geopolymers, while those containing 1% ramie fibre have the highest strength and lowest drying shrinkage.
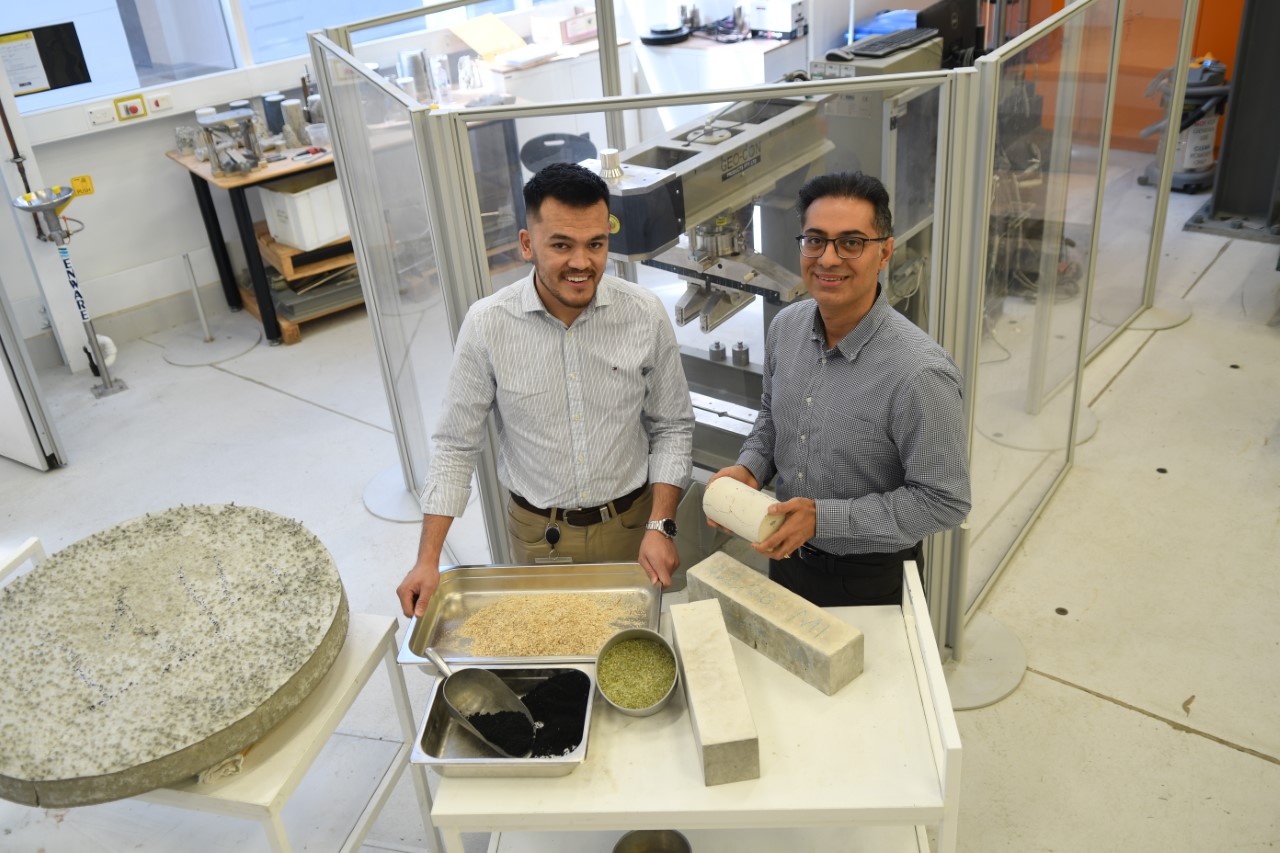
The new Australian-led study, published in the Construction and Building Materials journal (Vol 352, 17 October 2022), adds to global efforts tackling the environmental impact of producing conventional building materials and waste-to-landfill volumes.
“With concrete, we can not only recycle huge volumes of industrial by-products and waste materials, including concrete aggregates, to improve the mechanical and durability properties of concrete, but also use alternative eco-friendly natural fibres which otherwise would not be used constructively,” says Dr Gholampour.
“This research will also look to design mixes of recycled coarse aggregates and other types of cellulosic fibres including water paper, for different construction and building applications. We also plan to investigate their application in construction 3D printing for the future.”
The article – Mechanical and durability properties of natural fiber-reinforced geopolymers containing lead smelter slag and waste glass sand (2022) by Aliakbar Gholampour, Aamar Danish, Togay Ozbakkaloglu, Jung Heum Yeon and Osman Gencel – has been published in Construction and Building Materials DOI: 10.1016/j.conbuildmat.2022.129043. Also see this article and
‘Predicting ultimate condition and transition point on axial stress–strain curve of FRP-confined concrete using a meta-heuristic algorithm‘ (2023) by Ali Fallah Pour, Roohollah Shirani Faradonbeh, Aliakbar Gholampour and Tuan D Ngo published in Composite Structures DOI: 10.1016/j.compstruct.2022.116387.